LEDs convert electrical power into light output. During this process, heat is released as a byproduct. The primary cause of LED failure is often poor thermal management. Thus, any application utilising LEDs will need to consider how much heat is created by the LEDs, and how to manage this heat.
Unlike incandescent filament light bulbs, LEDs do not radiate heat directly from the LED itself. Rather they conduct heat from the PN junction to the thermal slug on the LED package. The thermal slug is not connected electrically but is soldered to the PCB. It sits beneath the LED die and draws the heat through it into the PCB board.
What Happens When an LED Overheats?
Typically, the maximum junction temperature for a standard LED is around 150°C. When LEDs exceed their optimal temperature, total LED failure can occur. But before the LED failure, other impacts to the LED parameters and performance can be seen. For example, did you know that LED colour and brightness are sensitive to temperature?
- Effects on dominant wavelength. Among other things, this is dependent on junction temperature. An increase in junction temperature can increase wavelengths, resulting in a slight colour shift.
- Effects on light output. A relationship exists between junction temperature and luminous flux. As temperatures increase, luminous flux will subsequently fall. Different wavelengths have various levels of sensitivity to this effect, with amber being the most sensitive.
- Effects on LED lifetime. LED reliability is a direct function of junction temperature. A higher junction temperature often leads to a reduced LED lifetime and lowered performance.
- Effects of forward voltage. This can cause issues when an LED is operated at constant voltage, when the temperature rises the forward voltage will drop, causing an increase in current which can then lead to variation in the brightness of the LEDs.
Methods of Thermal Management
Thermally managing LEDs by dispersing heat will help keep the LEDs operating efficiently. One of the most common methods of doing this is passive cooling by utilising heatsinks and thermal interface material (TIM), to conduct the excess heat and cool the LEDs. In this way the excess heat will be conducted from the LED junction to the heatsink, from where it is then radiated into the surrounding environment.
Heatsinking
A Heatsink is essentially a block of metal which performs as a passive device, drawing heat away from an electronic device and dispersing it into the air. The most common metals used for heatsinking are iron, aluminium and copper. Copper tends to have the highest thermal conductivity but is a much more expensive solution. Iron tends to have the lowest thermal conductivity. While aluminium still has a proficient level of thermal conductivity for a more cost-effective price. The shape and design of a heatsink are also key factors in enabling the cooling effect. A heatsink with extruded fins has a larger surface area is increased than one without. This means that heat can be radiated away more efficiently.
How TIM Enhances the Benefits of Heatsinking
Thermal interface material (TIM) fills the air pockets between the surface of the heatsink and the surface of the LED PCB. In doing so, TIM forms a continuous layer to conduct heat away more effectively from the LED to the heatsink. Thus, its use can further increase the benefits of a heatsink and enable your LEDs to operate efficiently for longer.
To show this effect in practice, we took a 1 LED Powerstar mounted to a heatsink and powered it for 30 minutes. After this time had elapsed, using a thermal camera we measured the temperature of the heatsink to determine how much heat had been drawn into it. We then repeated this exercise with the same set up but using a piece of TIM between the heatsink and the Powerstar.
From the snapshot below, it is clear that more heat has been drawn down into the heatsink when TIM has been used. With a difference of almost 8°C.
Left: LED Powerstar, heatsink and no TIM.
Right: LED Powerstar, heatsink and TIM.
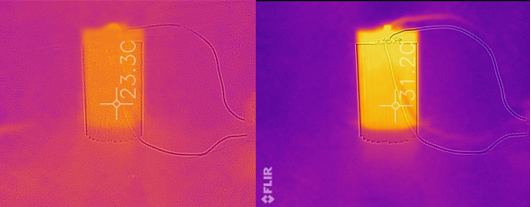
Related products: